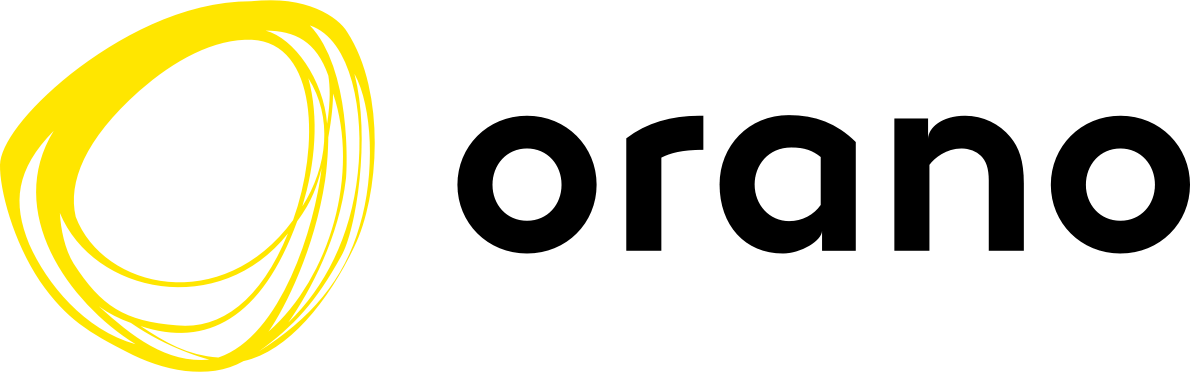
The conversion and enrichment operations are carried out across two sites, in Malvési and Tricastin. Underpinned by this unique integrated industrial platform and thanks to its upgraded facilities - Comurhex II for conversion and Georges Besse II for enrichment - Orano offers its customers the most modern infrastructures in the world, recognized across the market for its technical skills and state-of-the-art processes.
The only industrial players capable of receiving concentrates in all forms, with an industrial platform that also offers warehousing capacity in compliance with all authorizations held. It makes it possible to deploy custom-tailored services in accordance with customer needs: conversion, defluorination and denitration.
With its Comurhex II plants for conversion and the Georges Besse II plants for enrichment, the two major transformation activities have entered a new era. The modularity of Georges Besse II gives these two plants the potential to evolve according to market demand and needs.
Thanks to its safe, reliable and competitive European presence, Orano is able to secure supply for its customers' and the sustainability of its operations for the next 40 years.
Orano, a key player in uranium ore purification
Unparalleled : thanks to the superior performance of the facilities in Orano Malvési, the degree of purification is such that the process can address all forms of uranium ore, whatever its origin or degree of impurity.
Specialized in fluorine and uranium chemistry in all forms, the Tricastin site (Drôme), with 55 years of know-how, has become a reference industrial platform. Its activities include completing the transformation of UF4 into uranium hexafluoride (UF6), by adding 2 additional fluorine atoms before enrichment.
These past few years, Orano Malvési and Orano Tricastin have undergone considerable change, to renew their industrial equipment and improve the safety and competitiveness of the sites and the sector.
Comurhex II, heightened safety, in line with the latest standards
Launched in 2006, the Comurhex II program consisted of renewing three facilities at the Malvési site and building a new plant on the Tricastin site to replace Comurhex 1. The SEVESO High Threshold (ICPE) facility built to nuclear standards allows reinforced containment of the material: protected concrete buildings with autonomous ventilation, compartmentalization of the main building into 200 rooms, increased resistance safe shutdown earthquakes, and flood risk prevention.
From natural uranium to combustible uranium
To be usable as fuel in reactors, uranium must have a concentration of 2 to 5% uranium 235. Since natural uranium contains only 0.7%, enrichment operations will increase its concentration.
Separating uranium 235 and uranium 238 by centrifugation
Under the effect of centrifugal force, molecules are separated. This isotopic separation step is repeated in series. After these operations in cascade, the enriched UF6 is extracted directly into a suitable cylinder before solidifying in a dedicated station. The depleted UF6 is extracted into another cylinder which is also cooled.
Quality control of enriched UF6
The production of enriched UF6 is sampled then conditioned in cylinders to be shipped to the fuel manufacturer.
A high-performance technology with a smaller environmental footprint
Georges Besse II, a yield rate exceeding 99 %
After 50 years of experience in enrichment based on gaseous diffusion, enrichment continues at the Tricastin site, in the two new "Georges Besse II" plants using ultra-centrifugation technology.
The largest enrichment plant in Europe, Georges Besse II replaces the Eurodif plant, which for over 30 years produced uranium enriched via gaseous diffusion.
Commissioned in 2011, the plant reached its full capacity in end-2016. The first tests carried out confirm the facilities’ high performance levels, with yield rates in excess of 99%.
Its design enables operation according to the highest safety and security standards, in particular earthquake resistance, fire fighting and material containment.
Two different chemical processes are used to recover depleted uranium into uranium oxide (U3O8), in safe and easily storable forms.
Orano is the first manufacturer in the world to have fully refurbished its conversion plants to step up operational safety and reduce its environmental footprint. The new industrial facilities at the Malvési and Tricastin sites thus have innovative processes and use new technologies that enable it to minimize in its environmental footprint.